استفاده از درایرهای هوای فشرده در صنایع پتروشیمی و نفت و گاز نه تنها یک انتخاب بلکه یک ضرورت برای تضمین بهره وری ایمنی و پایداری عملیات محسوب می شود. هوای فشرده به عنوان چهارمین انرژی پرکاربرد در صنایع نقش حیاتی در بخش های مختلف این صنایع از جمله ابزار دقیق سیستم های کنترل پنوماتیک فرآیندهای تولید و انتقال مواد ایفا می کند.
وجود رطوبت و آلاینده ها در هوای فشرده می تواند منجر به خسارات جبران ناپذیری از جمله خوردگی تجهیزات اختلال در عملکرد ابزار دقیق توقف خطوط تولید کاهش کیفیت محصولات و افزایش هزینه های تعمیر و نگهداری شود. به همین دلیل استفاده از درایرهای هوای فشرده با حذف رطوبت و آلاینده ها هوای فشرده ای خشک تمیز و مطابق با استانداردهای بین المللی را فراهم می کند و از بروز مشکلات و خسارات احتمالی جلوگیری می کند.
در ادامه این مقاله به بررسی دقیق تر فواید استفاده از درایرهای هوای فشرده اصول عملکرد اجزای اصلی استانداردهای بین المللی تکنولوژی های پیشرفته و نکات فنی مهم در این زمینه خواهیم پرداخت.
اهمیت هوای خشک و تمیز در صنایع پتروشیمی و نفت و گاز
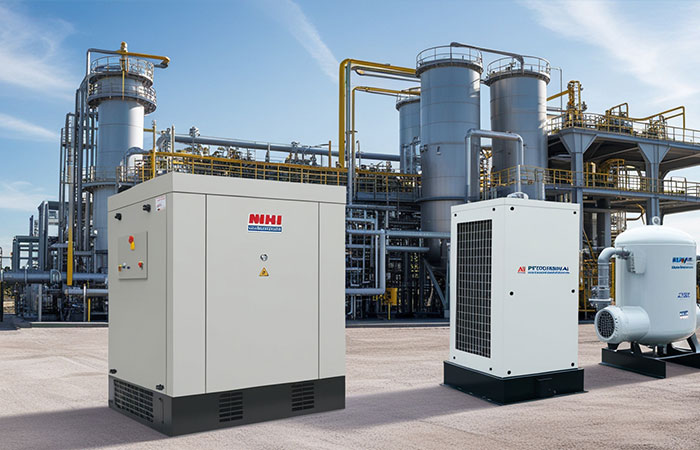
صنایع پتروشیمی و نفت و گاز به دلیل ماهیت حساس و پیچیده فرآیندهای تولید و انتقال مواد نیازمند استفاده از هوای فشرده ای با کیفیت بسیار بالا هستند. حضور رطوبت روغن ذرات معلق و سایر آلاینده ها در هوای فشرده می تواند اثرات مخربی بر تجهیزات فرآیندها و محصولات نهایی داشته باشد. برخی از مهم ترین اثرات منفی هوای مرطوب و آلوده در این صنایع عبارتند از :
- خوردگی و زنگ زدگی : رطوبت موجود در هوا با فلزات واکنش داده و باعث خوردگی و زنگ زدگی لوله ها شیرآلات سیلندرها ابزار دقیق و سایر تجهیزات پنوماتیک می شود. این امر منجر به کاهش عمر مفید تجهیزات افزایش هزینه های تعمیر و نگهداری و احتمال خرابی ناگهانی سیستم ها می شود.
- اختلال در عملکرد ابزار دقیق : رطوبت و آلاینده ها می توانند باعث کاهش دقت و حساسیت ابزار دقیق مانند سنسورها کنترلرها و شیرهای کنترلی شوند. این اختلال در عملکرد ابزار دقیق می تواند منجر به عدم کنترل دقیق فرآیندها کاهش کیفیت محصولات و افزایش ضایعات شود.
- یخ زدگی در دماهای پایین : در مناطق سردسیر و یا در فرآیندهایی که با دماهای پایین سروکار دارند رطوبت موجود در هوا می تواند یخ زده و باعث مسدود شدن لوله ها و شیرآلات پنوماتیک شود. این امر منجر به توقف خطوط تولید و اختلال در عملیات می شود.
- آلودگی محصولات : در برخی از فرآیندهای صنایع پتروشیمی و نفت و گاز هوای فشرده به طور مستقیم با مواد اولیه یا محصولات در تماس است. حضور رطوبت و آلاینده ها در هوای فشرده می تواند باعث آلودگی محصولات و کاهش کیفیت آن ها شود.
- افزایش هزینه های نگهداری : مشکلات ناشی از هوای مرطوب و آلوده مانند خوردگی اختلال در عملکرد تجهیزات و توقف خطوط تولید منجر به افزایش هزینه های نگهداری و تعمیرات می شود.
بنابراین استفاده از درایرهای هوای فشرده با حذف رطوبت و آلاینده ها هوای فشرده ای خشک تمیز و قابل اعتماد را فراهم می کند و از بروز مشکلات و خسارات احتمالی جلوگیری کرده و بهره وری ایمنی و پایداری عملیات را در صنایع پتروشیمی و نفت و گاز تضمین می کند.
اصول عملکرد انواع درایرهای هوای فشرده
درایرهای هوای فشرده بر اساس اصول مختلفی عمل می کنند و به طور کلی به سه دسته اصلی تقسیم می شوند :
- درایرهای تبریدی (Refrigerant Dryers) :
- اصل عملکرد : درایرهای تبریدی با خنک کردن هوای فشرده تا دمای نزدیک به نقطه انجماد آب (معمولاً بین ۲ تا ۱۰ درجه سانتیگراد) باعث تقطیر رطوبت موجود در هوا می شوند. هوای خنک شده از یک جداکننده رطوبت عبور کرده و قطرات آب تقطیر شده جدا می شوند. سپس هوای خشک شده گرم شده و به خط لوله منتقل می شود.
- اجزای اصلی :
- کمپرسور تبرید : برای خنک کردن مبرد و انتقال حرارت از هوای فشرده.
- مبدل حرارتی هوا به هوا : برای پیش خنک کردن هوای ورودی و گرم کردن هوای خروجی و افزایش راندمان انرژی.
- مبدل حرارتی هوا به مبرد (اواپراتور) : برای خنک کردن هوای فشرده توسط مبرد.
- جداکننده رطوبت : برای جدا کردن قطرات آب تقطیر شده از هوای فشرده.
- تخلیه خودکار کندانس : برای تخلیه اتوماتیک آب جمع شده در جداکننده رطوبت.
- مزایا :
- هزینه اولیه پایین تر نسبت به سایر انواع درایرها.
- عملکرد ساده و نگهداری آسان.
- مصرف انرژی نسبتاً کم.
- معایب :
- محدودیت در دستیابی به نقطه شبنم بسیار پایین (معمولاً نقطه شبنم فشاری حدود ۳ تا ۱۰ درجه سانتیگراد).
- عدم کارایی در دماهای بسیار پایین محیط.
- درایرهای جذبی (Desiccant Dryers) :
- اصل عملکرد : درایرهای جذبی با استفاده از مواد جاذب رطوبت (دسیکنت) مانند سیلیکاژل آلومینای فعال و غربال های مولکولی رطوبت موجود در هوای فشرده را جذب می کنند. هوای فشرده از بستر دسیکنت عبور کرده و رطوبت آن جذب می شود. برای احیای دسیکنت و حذف رطوبت جذب شده از روش های مختلفی مانند گرمایش کاهش فشار و یا ترکیبی از هر دو استفاده می شود. درایرهای جذبی معمولاً به صورت دو برج طراحی می شوند که در یک برج فرآیند جذب رطوبت انجام می شود و در برج دیگر فرآیند احیای دسیکنت.
- اجزای اصلی :
- برج های دسیکنت : حاوی مواد جاذب رطوبت (دسیکنت).
- شیرهای سوئیچینگ : برای هدایت جریان هوا بین برج ها و مراحل جذب و احیا.
- سیستم احیا : شامل گرمکن های الکتریکی یا هوای گرم (برای درایرهای جذبی با احیای حرارتی) یا سیستم وکیوم (برای درایرهای جذبی با احیای فشاری).
- فیلترهای غبارگیر : برای جلوگیری از ورود ذرات دسیکنت به خط لوله.
- انواع درایرهای جذبی :
- درایرهای جذبی با احیای حرارتی (Heat Regenerative Dryers) : از گرمای خارجی برای احیای دسیکنت استفاده می کنند.
- درایرهای جذبی بدون حرارت (Heatless Regenerative Dryers یا Pressure Swing Adsorption – PSA Dryers) : از بخشی از هوای خشک شده برای احیای دسیکنت با کاهش فشار استفاده می کنند.
- درایرهای جذبی دمنده (Blower Purge Dryers) : از دمنده برای عبور هوای محیط گرم شده از بستر دسیکنت و احیای آن استفاده می کنند.
- مزایا :
- دستیابی به نقطه شبنم بسیار پایین (تا -۴۰ درجه سانتیگراد و پایین تر).
- مناسب برای کاربردهایی که نیاز به هوای بسیار خشک دارند.
- قابلیت کارکرد در دماهای پایین محیط.
- معایب :
- هزینه اولیه بالاتر نسبت به درایرهای تبریدی.
- مصرف انرژی بیشتر به خصوص در درایرهای جذبی با احیای حرارتی.
- نیاز به نگهداری بیشتر و تعویض دوره ای دسیکنت.
- افت فشار بیشتر در مقایسه با درایرهای تبریدی.
- درایرهای غشایی (Membrane Dryers) :
- اصل عملکرد : درایرهای غشایی از غشاهای پلیمری نیمه تراوا استفاده می کنند که به طور انتخابی بخار آب را از هوای فشرده عبور می دهند. هوای فشرده از داخل فیبرهای توخالی غشا عبور می کند و بخار آب به دلیل اختلاف فشار جزئی بخار آب بین داخل و خارج غشا از دیواره غشا عبور کرده و به بیرون هدایت می شود. هوای خشک شده از انتهای فیبرها خارج می شود. بخشی از هوای خشک شده (purge air) برای کمک به دفع رطوبت از سطح خارجی غشا استفاده می شود.
- اجزای اصلی :
- ماژول غشایی : حاوی فیبرهای توخالی غشای پلیمری.
- فیلترهای ورودی و خروجی : برای جلوگیری از ورود ذرات و آلاینده ها به ماژول غشایی.
- رگولاتور فشار و فلومتر : برای کنترل فشار و جریان هوای purge.
- مزایا :
- اندازه کوچک و وزن سبک.
- عملکرد بی صدا و بدون لرزش.
- عدم نیاز به برق و قطعات متحرک.
- نگهداری کم و عمر طولانی.
- معایب :
- هزینه اولیه بالاتر نسبت به درایرهای تبریدی.
- نقطه شبنم محدودتر نسبت به درایرهای جذبی (معمولاً نقطه شبنم فشاری حدود ۱۰ تا ۲۰ درجه سانتیگراد).
- مصرف هوای purge و کاهش راندمان انرژی.
- حساسیت به روغن و آلاینده های دیگر.
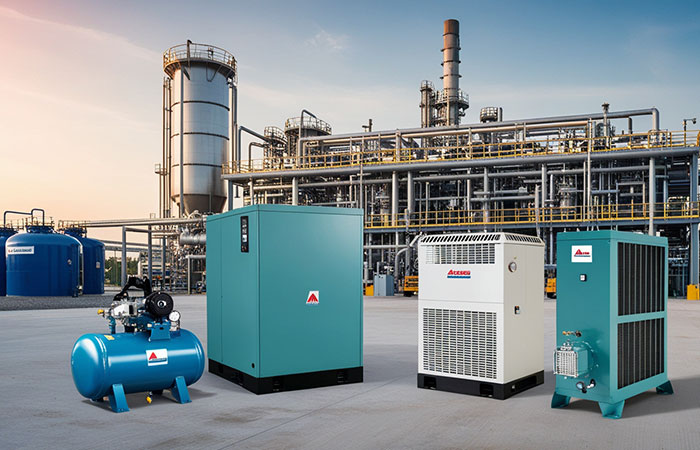
فواید استفاده از درایرهای هوای فشرده در صنایع پتروشیمی و نفت و گاز
استفاده از درایرهای هوای فشرده در صنایع پتروشیمی و نفت و گاز فواید متعددی را به همراه دارد که در ادامه به برخی از مهم ترین آن ها اشاره می شود :
- افزایش طول عمر تجهیزات : با حذف رطوبت و جلوگیری از خوردگی و زنگ زدگی عمر مفید تجهیزات پنوماتیک ابزار دقیق و سایر دستگاه های حساس به رطوبت به طور چشمگیری افزایش می یابد. این امر منجر به کاهش هزینه های جایگزینی و تعمیرات می شود.
- بهبود عملکرد و دقت ابزار دقیق : هوای خشک و تمیز باعث عملکرد دقیق تر و پایدارتر ابزار دقیق و سیستم های کنترلی می شود. این امر منجر به کنترل بهتر فرآیندها افزایش کیفیت محصولات و کاهش ضایعات می شود.
- کاهش خرابی و توقف خطوط تولید : با جلوگیری از یخ زدگی خوردگی و اختلال در عملکرد تجهیزات احتمال خرابی و توقف ناگهانی خطوط تولید به طور قابل ملاحظه ای کاهش می یابد. این امر منجر به افزایش بهره وری و کاهش هزینه های ناشی از توقف تولید می شود.
- بهبود کیفیت محصولات : در فرآیندهایی که هوای فشرده با مواد اولیه یا محصولات در تماس است استفاده از هوای خشک و تمیز از آلودگی محصولات و کاهش کیفیت آن ها جلوگیری می کند.
- کاهش هزینه های نگهداری و تعمیرات : با کاهش خوردگی خرابی تجهیزات و توقف خطوط تولید هزینه های نگهداری و تعمیرات کمپرسور ها به طور قابل توجهی کاهش می یابد.
- افزایش ایمنی : هوای خشک و تمیز باعث عملکرد ایمن تر تجهیزات پنوماتیک و سیستم های کنترلی می شود و احتمال حوادث ناشی از خرابی تجهیزات را کاهش می دهد.
- کاهش مصرف انرژی : در برخی موارد استفاده از درایرهای هوای فشرده می تواند منجر به کاهش مصرف انرژی در سیستم هوای فشرده شود. به عنوان مثال هوای خشک باعث کاهش اصطکاک در سیستم های پنوماتیک و بهبود راندمان ابزار پنوماتیک می شود.
- رعایت استانداردهای بین المللی : استفاده از درایرهای هوای فشرده به صنایع پتروشیمی و نفت و گاز کمک می کند تا استانداردهای بین المللی کیفیت هوای فشرده مانند ISO ۸۵۷۳-۱ را رعایت کنند.
کاربردهای درایرهای هوای فشرده در صنایع پتروشیمی و نفت و گاز
درایرهای هوای فشرده در بخش های مختلف صنایع پتروشیمی و نفت و گاز کاربردهای گسترده ای دارند که برخی از مهم ترین آن ها عبارتند از :
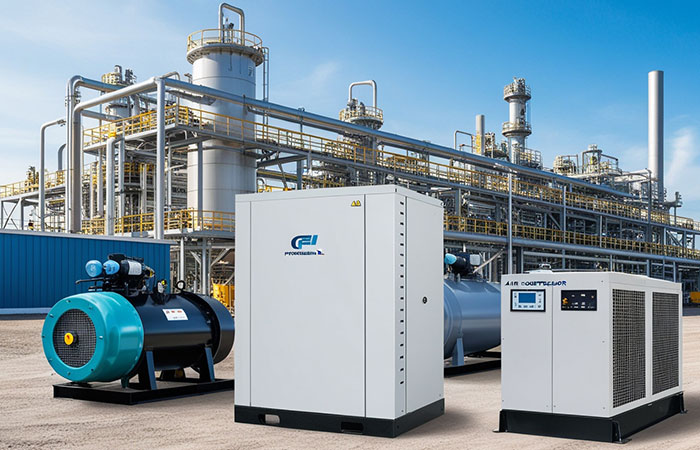
- هوای ابزار دقیق (Instrument Air) : هوای خشک و تمیز برای سیستم های ابزار دقیق و کنترل پنوماتیک بسیار حیاتی است. درایرهای جذبی به دلیل توانایی دستیابی به نقطه شبنم بسیار پایین انتخاب ایده آلی برای تامین هوای ابزار دقیق در این صنایع هستند.
- سیستم های کنترل پنوماتیک : درایرهای هوای فشرده برای تامین هوای خشک و تمیز برای سیستم های کنترل پنوماتیک در پالایشگاه ها پتروشیمی ها و سکوهای نفتی استفاده می شوند.
- فرآیندهای تولید : در برخی از فرآیندهای تولید مواد شیمیایی و پتروشیمی هوای فشرده به عنوان بخشی از فرآیند مورد استفاده قرار می گیرد. در این موارد استفاده از درایرهای هوای فشرده برای اطمینان از کیفیت هوای فرآیندی ضروری است.
- انتقال مواد : هوای فشرده در سیستم های انتقال مواد پودری و گرانولی در صنایع پتروشیمی کاربرد دارد. استفاده از هوای خشک از چسبندگی مواد و گرفتگی لوله ها جلوگیری می کند.
- نیوماتیک و ابزارهای پنوماتیک : درایرهای هوای فشرده برای تامین هوای خشک و تمیز برای ابزارهای پنوماتیک مورد استفاده در تعمیر و نگهداری و عملیات نصب و راه اندازی در صنایع پتروشیمی و نفت و گاز استفاده می شوند.
- خشک کردن خطوط لوله و تجهیزات : پس از تست های هیدرواستاتیک یا تعمیرات خطوط لوله و تجهیزات نیاز به خشک شدن دارند. هوای خشک تولید شده توسط درایرها برای خشک کردن سریع و موثر خطوط لوله و تجهیزات استفاده می شود.
- سیستم های ایمنی : در برخی از سیستم های ایمنی مانند سیستم های تنفسی اضطراری هوای فشرده خشک و تمیز مورد نیاز است.
استانداردهای بین المللی و تکنولوژی های پیشرفته
استانداردهای بین المللی نقش مهمی در تضمین کیفیت هوای فشرده در صنایع مختلف ایفا می کنند. مهم ترین استاندارد در این زمینه ISO ۸۵۷۳-۱ است که کیفیت هوای فشرده را بر اساس غلظت آلاینده های مختلف مانند ذرات جامد رطوبت و روغن طبقه بندی می کند. صنایع پتروشیمی و نفت و گاز معمولاً نیازمند هوای فشرده ای با کیفیت بسیار بالا هستند و باید از درایرهای هوای فشرده ای استفاده کنند که بتوانند این استانداردها را برآورده کنند.
در زمینه تکنولوژی های پیشرفته در درایرهای هوای فشرده می توان به موارد زیر اشاره کرد :
- درایرهای هیبریدی : این درایرها از ترکیب دو یا چند تکنولوژی خشک کننده (مانند تبریدی و جذبی) برای دستیابی به راندمان بالاتر و مصرف انرژی کمتر استفاده می کنند.
- درایرهای هوشمند : این درایرها مجهز به سیستم های کنترل هوشمند و سنسورهای پیشرفته هستند که عملکرد درایر را به طور مداوم پایش کرده و بهینه سازی می کنند. این سیستم ها می توانند داده های عملکرد را جمع آوری و تجزیه و تحلیل کرده و اطلاعات مفیدی را برای نگهداری پیشگیرانه و بهبود راندمان انرژی ارائه دهند.
- درایرهای با راندمان انرژی بالا : تولیدکنندگان درایرهای هوای فشرده به طور مداوم در حال توسعه تکنولوژی هایی برای کاهش مصرف انرژی و افزایش راندمان درایرها هستند. استفاده از کمپرسورهای تبرید با راندمان بالا مواد دسیکنت جدید با ظرفیت جذب بیشتر و سیستم های احیای بهینه از جمله این تکنولوژی ها هستند.
- درایرهای قابل حمل و ماژولار : برای کاربردهای خاص مانند تعمیرات خطوط لوله در مناطق دورافتاده درایرهای هوای فشرده قابل حمل و ماژولار توسعه یافته اند که امکان جابجایی و نصب آسان را فراهم می کنند.
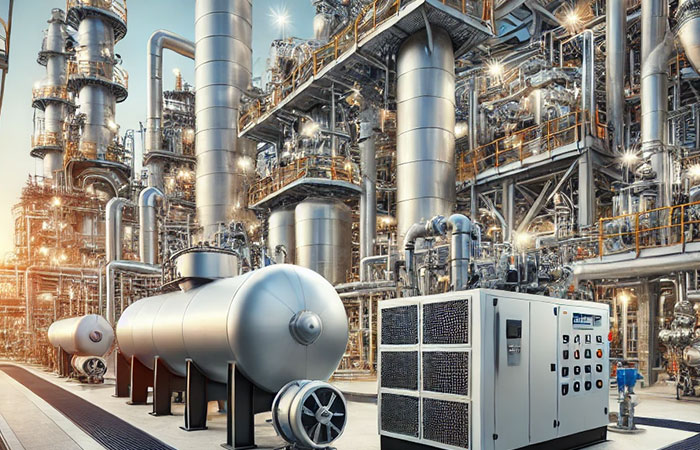
نکات فنی مهم در انتخاب و نگهداری درایرهای هوای فشرده
انتخاب و نگهداری صحیح درایرهای هوای فشرده برای اطمینان از عملکرد مطلوب و طول عمر طولانی آن ها بسیار مهم است. برخی از نکات فنی مهم در این زمینه عبارتند از :
- تعیین نقطه شبنم مورد نیاز : نقطه شبنم مورد نیاز هوای فشرده بستگی به نوع کاربرد و شرایط محیطی دارد. برای کاربردهای حساس مانند هوای ابزار دقیق در مناطق سردسیر نقطه شبنم بسیار پایین مورد نیاز است.
- محاسبه دبی هوای مورد نیاز : ظرفیت درایر باید متناسب با دبی هوای فشرده مورد نیاز سیستم باشد. انتخاب درایر با ظرفیت کمتر از نیاز سیستم منجر به عدم کارایی و آسیب به درایر می شود.
- انتخاب نوع درایر مناسب : نوع درایر (تبریدی جذبی یا غشایی) باید بر اساس نقطه شبنم مورد نیاز شرایط محیطی هزینه اولیه هزینه بهره برداری و فضای موجود انتخاب شود.
- نصب صحیح درایر : درایر باید در مکانی مناسب با تهویه کافی و دسترسی آسان برای نگهداری نصب شود. همچنین باید از فیلترهای مناسب در ورودی و خروجی درایر استفاده شود.
- نگهداری منظم : نگهداری منظم درایر شامل بازدیدهای دوره ای تعویض فیلترها تخلیه کندانس بررسی عملکرد اجزای اصلی و سرویس دوره ای کمپرسور تبرید (در درایرهای تبریدی) است.
- مانیتورینگ عملکرد : مانیتورینگ عملکرد درایر از طریق سنسورهای دما فشار و نقطه شبنم و سیستم های کنترل هوشمند به شناسایی زودهنگام مشکلات و جلوگیری از خرابی های ناگهانی کمک می کند.
- آموزش پرسنل : پرسنل مسئول بهره برداری و نگهداری درایرهای هوای فشرده باید آموزش های لازم را در زمینه عملکرد نگهداری و عیب یابی این تجهیزات دیده باشند.
نتیجه گیری
استفاده از درایرهای هوای فشرده در صنایع پتروشیمی و نفت و گاز یک سرمایه گذاری ضروری برای تضمین بهره وری ایمنی و پایداری عملیات است. درایرهای هوای فشرده با حذف رطوبت و آلاینده ها هوای فشرده ای خشک تمیز و مطابق با استانداردهای بین المللی را فراهم می کنند و از بروز مشکلات و خسارات احتمالی جلوگیری می کنند. انتخاب صحیح نوع درایر نصب اصولی و نگهداری منظم کلید دستیابی به حداکثر فواید استفاده از این تجهیزات حیاتی در صنایع پتروشیمی و نفت و گاز است. با توجه به پیشرفت های تکنولوژی در زمینه درایرهای هوای فشرده صنایع پتروشیمی و نفت و گاز می توانند با بهره گیری از تکنولوژی های نوین راندمان سیستم هوای فشرده خود را بهبود بخشیده و هزینه های انرژی و نگهداری را کاهش دهند.
پرسش و پاسخ متداول کاربران
۱. چه نوع درایری برای هوای ابزار دقیق در یک پالایشگاه مناسب تر است؟
برای هوای ابزار دقیق در پالایشگاه ها درایرهای جذبی به دلیل توانایی دستیابی به نقطه شبنم بسیار پایین و اطمینان از هوای کاملاً خشک مناسب ترین گزینه هستند. درایرهای جذبی با احیای حرارتی یا بدون حرارت می توانند نقطه شبنم مورد نیاز برای ابزار دقیق حساس را تامین کنند و از عملکرد صحیح و پایدار سیستم های کنترل پنوماتیک اطمینان حاصل نمایند.
۲. چگونه می توان راندمان انرژی درایرهای جذبی را بهبود بخشید؟
برای بهبود راندمان انرژی درایرهای جذبی می توان از روش های مختلفی استفاده کرد از جمله :
استفاده از درایرهای جذبی با احیای دمنده (Blower Purge Dryers) : این درایرها نسبت به درایرهای جذبی با احیای حرارتی و بدون حرارت مصرف هوای purge کمتری دارند.
بهینه سازی سیکل احیا : تنظیم دقیق زمان و دمای احیا و استفاده از سیستم های کنترل هوشمند می تواند مصرف انرژی را کاهش دهد.
بازیابی حرارت احیا : در درایرهای جذبی با احیای حرارتی می توان از سیستم های بازیابی حرارت برای استفاده مجدد از گرمای هوای خروجی از سیکل احیا استفاده کرد.
انتخاب دسیکنت مناسب : استفاده از دسیکنت های جدید با ظرفیت جذب رطوبت بیشتر و نیاز به دمای احیای پایین تر می تواند راندمان انرژی را بهبود بخشد.
۳. چه استانداردهایی برای کیفیت هوای فشرده در صنایع پتروشیمی و نفت و گاز باید رعایت شود؟
مهم ترین استاندارد برای کیفیت هوای فشرده در صنایع پتروشیمی و نفت و گاز ISO ۸۵۷۳-۱ است. این استاندارد کیفیت هوا را بر اساس غلظت ذرات جامد رطوبت و روغن طبقه بندی می کند. صنایع پتروشیمی و نفت و گاز معمولاً نیازمند هوای فشرده ای با کلاس کیفیتی بالا (مانند کلاس ۱.۴.۱ یا ۱.۲.۱ مطابق با ISO ۸۵۷۳-۱) هستند. انتخاب درایرهای هوای فشرده و سیستم های فیلتراسیون مناسب باید بر اساس الزامات این استاندارد انجام شود تا کیفیت هوای فشرده مطابق با نیازهای فرآیندها و تجهیزات تضمین گردد.