عملکرد بی وقفه و قابل اعتماد کمپرسورهای اسکرو شریان حیاتی بسیاری از صنایع مدرن است. تضمین این عملکرد مستلزم نگهداری دقیق و منظم است. پنج نکته کلیدی زیر به شما کمک می کند تا با رویکردی علمی و مهندسی طول عمر و بازدهی کمپرسورهای اسکروی خود را به حداکثر برسانید.
کمپرسورهای اسکرو + قلب تپنده صنایع مدرن و تعریف عملکرد فنی آن ها
کمپرسورهای اسکرو به عنوان یکی از پرکاربردترین انواع کمپرسورهای جابجایی مثبت نقش حیاتی در تامین هوای فشرده مورد نیاز صنایع گوناگون ایفا می کنند. عملکرد فنی این کمپرسورها بر مبنای اصل جابجایی مثبت دورانی استوار است. در این مکانیزم هوا در فضای بین دو روتور مارپیچی (یکی نر و دیگری ماده) به دام افتاده و با چرخش روتورها حجم این فضا به تدریج کاهش می یابد. این کاهش حجم منجر به افزایش فشار هوا شده و در نهایت هوای فشرده از خروجی کمپرسور تخلیه می شود.
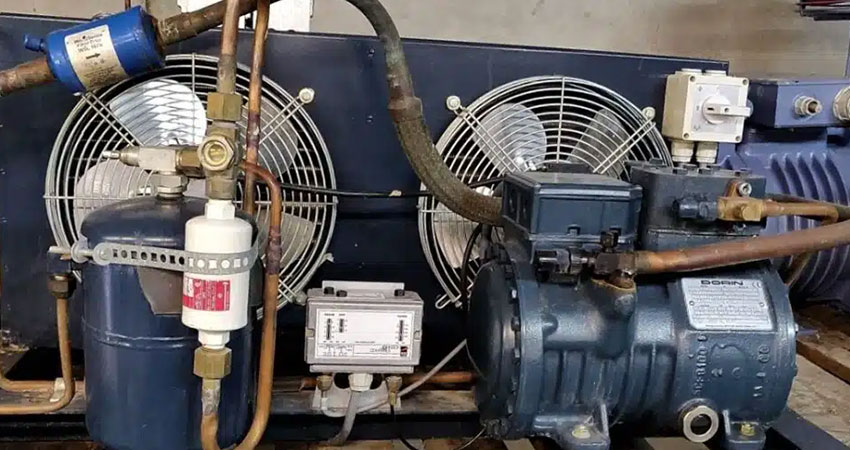
در یک کمپرسور اسکرو روغنی (Oil Inject Screw Compressor) روغن نقش چندگانه ای ایفا می کند : خنک کاری روانکاری و آب بندی. روغن به فضای کمپرسور تزریق شده و گرمای ناشی از تراکم هوا را جذب می کند اصطکاک بین قطعات متحرک را کاهش داده و فضای بین روتورها را آب بندی می کند تا از نشتی هوا و کاهش راندمان جلوگیری شود. پس از خروج هوا و روغن از واحد هواساز (Air End) مخلوط هوا و روغن از طریق سپراتور روغن (Oil Separator) از هم جدا می شوند. روغن جدا شده پس از خنک شدن و فیلتراسیون مجدد به سیکل کمپرسور باز می گردد.
در مقابل کمپرسورهای اسکرو خشک (Oil-Free Screw Compressor) فاقد سیستم روغن کاری در محفظه تراکم هستند. تراکم هوا در این کمپرسورها صرفاً از طریق چرخش روتورها و بدون حضور روغن انجام می پذیرد. این نوع کمپرسورها برای کاربردهایی که نیاز به هوای فشرده کاملاً عاری از روغن دارند مانند صنایع دارویی غذایی و الکترونیک ایده آل هستند. برای دستیابی به هوای فشرده بدون روغن کمپرسورهای اسکرو خشک معمولاً از دو یا چند مرحله تراکم بهره می برند و از پوشش های خاصی بر روی روتورها و محفظه برای کاهش اصطکاک و سایش استفاده می کنند.
اجزای اصلی و اصول کارکرد + کالبد شکافی یک کمپرسور اسکرو
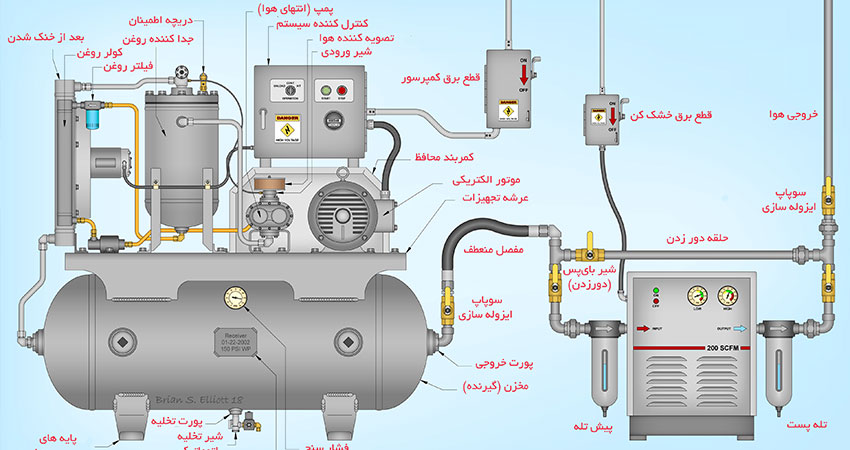
درک عملکرد اجزای اصلی کمپرسور اسکرو کلید نگهداری موثر و بهینه سازی عملکرد آن است. اجزای کلیدی یک کمپرسور اسکرو عبارتند از :
- واحد هواساز (Air End) : قلب کمپرسور اسکرو که تراکم هوا در آن انجام می شود. واحد هواساز شامل روتورهای مارپیچی (معمولاً روتور نر و ماده) محفظه (Casing) و بیرینگ ها (Bearings) است. پروفیل روتورها (Rotor Profile) طراحی هندسی پیچیده ای است که نقش اساسی در راندمان ظرفیت و سطح صدای کمپرسور دارد. پروفیل های پیشرفته تر مانند پروفیل های “Σ” و “High Efficiency” با کاهش نشتی داخلی و بهبود انتقال حرارت به افزایش راندمان و کاهش مصرف انرژی کمک می کنند. جنس روتورها معمولاً از فولاد آلیاژی با دقت ماشین کاری بالا و پوشش های مقاوم در برابر سایش (مانند پوشش های کامپوزیتی یا سرامیکی در کمپرسورهای خشک) انتخاب می شود. بیرینگ ها نقش حیاتی در تحمل بارهای محوری و شعاعی روتورها و تضمین چرخش روان و بدون لرزش آن ها دارند. انتخاب بیرینگ های با کیفیت و روانکاری مناسب طول عمر واحد هواساز را به طور چشمگیری افزایش می دهد.
- سیستم روغن کاری (Lubrication System) (در کمپرسورهای روغنی) : این سیستم وظیفه تامین روغن به واحد هواساز برای خنک کاری روانکاری و آب بندی را بر عهده دارد. اجزای اصلی آن شامل مخزن روغن (Oil Reservoir) پمپ روغن (Oil Pump) فیلتر روغن (Oil Filter) خنک کن روغن (Oil Cooler) و سپراتور روغن (Oil Separator) است. کیفیت روغن نقش بسیار مهمی در عملکرد و طول عمر کمپرسور دارد. روغن های سینتتیک با کیفیت بالا پایداری حرارتی و اکسیداسیون بهتری دارند و می توانند در دماهای بالاتر و برای مدت زمان طولانی تری کار کنند. فیلتر روغن وظیفه حذف ذرات معلق و آلودگی ها از روغن را بر عهده دارد و باید به طور منظم تعویض شود تا از آسیب به اجزای حساس سیستم روغن کاری جلوگیری شود. سپراتور روغن با استفاده از مکانیزم های مختلف (مانند جداسازی گرانشی سانتریفیوژی یا فیلتراسیون) روغن را از هوای فشرده جدا می کند. راندمان سپراتور روغن تاثیر مستقیمی بر کیفیت هوای فشرده و میزان روغن مصرفی کمپرسور دارد.
- سیستم خنک کننده (Cooling System) : سیستم خنک کننده وظیفه دفع حرارت تولید شده در فرآیند تراکم و حفظ دمای کاری کمپرسور در محدوده مجاز را بر عهده دارد. کمپرسورهای اسکرو معمولاً از دو نوع سیستم خنک کننده استفاده می کنند : هوا خنک (Air-Cooled) و آب خنک (Water-Cooled). در سیستم هوا خنک فن های پرقدرت هوا را از روی رادیاتورهای خنک کننده عبور داده و حرارت را به محیط منتقل می کنند. سیستم های آب خنک از مبدل های حرارتی استفاده می کنند که آب خنک کننده در آن ها جریان یافته و حرارت را از روغن یا هوای فشرده جذب می کند. انتخاب سیستم خنک کننده مناسب بستگی به شرایط محیطی ظرفیت کمپرسور و الزامات کاربرد دارد. نگهداری صحیح سیستم خنک کننده شامل تمیز کردن رادیاتورها بررسی سطح مایع خنک کننده (در سیستم های آب خنک) و اطمینان از عملکرد صحیح فن ها است.
- سیستم کنترل (Control System) : سیستم کنترل وظیفه مدیریت و پایش عملکرد کمپرسور را بر عهده دارد. سیستم های کنترل مدرن از کنترلرهای منطقی قابل برنامه ریزی (PLC) و سنسورهای دقیق برای اندازه گیری پارامترهای مختلف مانند فشار دما جریان و سطح روغن استفاده می کنند. سیستم کنترل می تواند عملکرد کمپرسور را بهینه کند مصرف انرژی را کاهش دهد و از بروز خرابی های احتمالی جلوگیری کند. ویژگی های پیشرفته سیستم های کنترل شامل کنترل دور متغیر (VSD) مانیتورینگ از راه دور و قابلیت اتصال به سیستم های مدیریت ساختمان (BMS) است. کنترل دور متغیر با تنظیم سرعت موتور کمپرسور بر اساس میزان هوای فشرده مورد نیاز به طور قابل توجهی مصرف انرژی را کاهش می دهد. مانیتورینگ از راه دور امکان پایش عملکرد کمپرسور از طریق اینترنت یا شبکه های محلی را فراهم می کند و به تشخیص سریع تر مشکلات و انجام اقدامات پیشگیرانه کمک می کند.
- سیستم ورودی و خروجی هوا (Air Inlet and Outlet System) : این سیستم شامل اجزایی است که کیفیت هوای ورودی و خروجی کمپرسور را بهبود می بخشند. فیلتر هوای ورودی (Air Inlet Filter) وظیفه حذف ذرات گرد و غبار و آلودگی ها از هوای ورودی را بر عهده دارد و از ورود آلودگی به واحد هواساز جلوگیری می کند. سپراتور آب و روغن (Moisture Separator & Oil Separator) (در سیستم خروجی) وظیفه حذف قطرات آب و روغن باقی مانده در هوای فشرده را بر عهده دارد و کیفیت هوای فشرده را مطابق با استانداردهای مورد نیاز بهبود می بخشد. درایرهای جذبی (Desiccant Dryers) و تبریدی (Refrigerant Dryers) برای کاهش رطوبت هوای فشرده و جلوگیری از تشکیل کندانس و خوردگی در سیستم لوله کشی هوای فشرده استفاده می شوند. مخازن هوای فشرده (Air Receivers) برای ذخیره سازی هوای فشرده کاهش پالس های فشار و تامین هوای فشرده پایدار به سیستم مصرف کننده استفاده می شوند.
کاربردهای صنعتی گسترده + از خطوط تولید تا نیروگاه ها
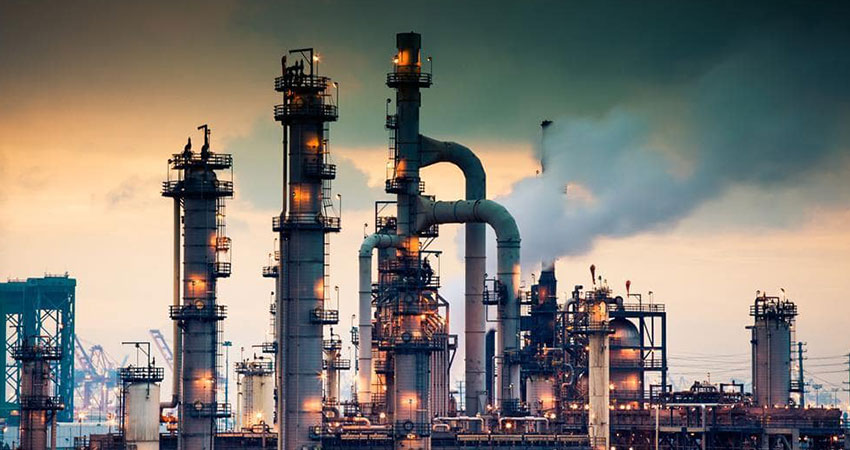
کمپرسورهای اسکرو به دلیل قابلیت اطمینان بالا راندمان مناسب و تنوع ظرفیت در طیف وسیعی از صنایع کاربرد دارند. برخی از مهم ترین کاربردهای صنعتی عبارتند از :
- صنایع تولیدی و کارخانجات : تامین هوای فشرده برای ابزارهای پنوماتیک (Pneumatic Tools) سیستم های اتوماسیون (Automation Systems) خطوط تولید (Production Lines) سیستم های انتقال مواد (Material Handling Systems) و رنگ پاشی (Painting). در این صنایع کمپرسورهای اسکرو نقش کلیدی در افزایش بهره وری و کاهش هزینه های تولید ایفا می کنند. به عنوان مثال در صنعت خودروسازی کمپرسورهای اسکرو در خطوط مونتاژ ربات های جوشکاری و سیستم های رنگ پاشی به طور گسترده استفاده می شوند. در صنعت نساجی هوای فشرده برای ماشین آلات بافندگی و ریسندگی سیستم های تمیزکاری و کنترل رطوبت استفاده می شود.
- صنایع نفت گاز و پتروشیمی : تامین هوای فشرده برای ابزار دقیق (Instrument Air) سیستم های کنترل فرآیند (Process Control Systems) سیستم های ایمنی (Safety Systems) راه اندازی توربین های گازی (Gas Turbine Startup) و انتقال گاز (Gas Transmission). در این صنایع قابلیت اطمینان و ایمنی کمپرسورها از اهمیت ویژه ای برخوردار است. کمپرسورهای اسکرو مورد استفاده در صنایع نفت و گاز معمولاً مطابق با استانداردهای سخت گیرانه API و ISO طراحی و تولید می شوند و از مواد مقاوم در برابر خوردگی و شرایط محیطی سخت ساخته می شوند.
- صنایع نیروگاهی : تامین هوای فشرده برای سیستم های کنترل و ابزار دقیق نیروگاه (Power Plant Control & Instrumentation) سیستم های احتراق (Combustion Systems) سیستم های تمیزکاری (Cleaning Systems) و راه اندازی توربین های گازی (Gas Turbine Startup). در نیروگاه های سیکل ترکیبی کمپرسورهای اسکرو در سیستم های هوای ورودی توربین گازی نیز کاربرد دارند.
- صنایع غذایی و دارویی : تامین هوای فشرده بدون روغن (Oil-Free Compressed Air) برای فرآیندهای تولید بسته بندی و پر کردن مواد غذایی و دارویی. در این صنایع کیفیت هوای فشرده از اهمیت بسیار بالایی برخوردار است و باید مطابق با استانداردهای بهداشتی سخت گیرانه باشد. کمپرسورهای اسکرو خشک به دلیل تولید هوای فشرده کاملاً عاری از روغن گزینه ایده آلی برای این کاربردها هستند.
- صنایع پزشکی و بیمارستانی : تامین هوای طبی (Medical Air) برای دستگاه های تنفسی تجهیزات دندانپزشکی و سایر تجهیزات پزشکی. هوای طبی باید مطابق با استاندارد ISO ۷۳۹۶-۱ و فارماکوپه (Pharmacopoeia) باشد و از نظر خلوص رطوبت و آلودگی های میکروبی کنترل شده باشد. کمپرسورهای اسکرو خشک و سیستم های تصفیه هوای طبی پیشرفته هوای طبی با کیفیت بالا را برای بیمارستان ها و مراکز درمانی تامین می کنند.
- صنایع معدنی و سیمان : تامین هوای فشرده برای ابزارهای حفاری (Drilling Tools) سیستم های انتقال مواد (Material Handling Systems) سیستم های پنوماتیک (Pneumatic Systems) و عملیات انفجار (Blasting Operations). کمپرسورهای اسکرو مورد استفاده در این صنایع باید مقاوم در برابر شرایط سخت محیطی گرد و غبار و لرزش باشند.
بیشتر بخوانید:
مقایسه کمپرسورهای هوای پیستونی و اسکرو
استانداردهای بین المللی و فناوری های پیشرفته + تضمین کیفیت و کارایی
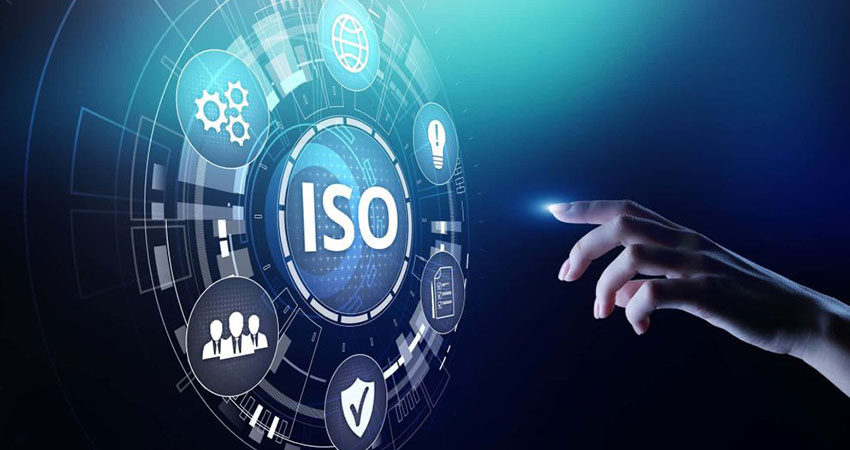
رعایت استانداردهای بین المللی و بهره گیری از فناوری های پیشرفته نقش کلیدی در تضمین کیفیت کارایی و ایمنی کمپرسورهای اسکرو دارد. برخی از مهم ترین استانداردها و فناوری های مرتبط عبارتند از :
- استاندارد ISO ۸۵۷۳–۱ : این استاندارد بین المللی کیفیت هوای فشرده را بر اساس سه پارامتر اصلی : ذرات جامد آب و روغن طبقه بندی می کند. صنایع مختلف بر اساس نوع کاربرد خود به سطوح مختلفی از کیفیت هوای فشرده نیاز دارند. به عنوان مثال صنایع غذایی و دارویی به هوای فشرده کلاس ۱ (بسیار خالص) نیاز دارند در حالی که صنایع عمومی ممکن است به هوای فشرده کلاس ۳ یا ۴ نیاز داشته باشند. انتخاب کمپرسور و سیستم تصفیه هوای فشرده مناسب بر اساس استاندارد ISO ۸۵۷۳-۱ تضمین می کند که هوای فشرده مطابق با الزامات کاربرد تامین شود.
- استاندارد ISO ۱۲۱۷ : این استاندارد بین المللی روش های آزمایش و اندازه گیری عملکرد کمپرسورهای جابجایی مثبت را مشخص می کند. استاندارد ISO ۱۲۱۷ پارامترهای مهمی مانند ظرفیت حجمی (Volume Flow Rate) فشار کاری (Working Pressure) مصرف توان (Power Consumption) و راندمان ایزوترمال (Isothermal Efficiency) را تعریف می کند. تست و اندازه گیری عملکرد کمپرسورها بر اساس استاندارد ISO ۱۲۱۷ امکان مقایسه عملکرد کمپرسورهای مختلف و اطمینان از انطباق عملکرد واقعی با مشخصات فنی اعلام شده توسط سازنده را فراهم می کند.
- استاندارد ISO ۱۱۰۱۱ : این استاندارد بین المللی راهنمایی برای ارزیابی بهره وری انرژی سیستم های هوای فشرده ارائه می دهد. استاندارد ISO ۱۱۰۱۱ روش های مختلفی برای اندازه گیری و تحلیل مصرف انرژی سیستم های هوای فشرده شناسایی فرصت های بهبود بهره وری انرژی و محاسبه صرفه جویی انرژی ناشی از اقدامات بهینه سازی را ارائه می دهد. پیاده سازی سیستم مدیریت انرژی بر اساس استاندارد ISO ۱۱۰۱۱ به صنایع کمک می کند تا مصرف انرژی سیستم های هوای فشرده خود را کاهش داده و هزینه های عملیاتی را به طور قابل توجهی کاهش دهند.
- فناوری درایو سرعت متغیر (VSD) : کمپرسورهای اسکرو مجهز به درایو سرعت متغیر (Variable Speed Drive) با تنظیم سرعت موتور بر اساس میزان هوای فشرده مورد نیاز مصرف انرژی را به طور چشمگیری کاهش می دهند. در سیستم های هوای فشرده سنتی با سرعت ثابت کمپرسورها با حداکثر سرعت کار می کنند حتی زمانی که تقاضای هوای فشرده کم است. این امر منجر به اتلاف انرژی قابل توجهی می شود. فناوری VSD با انطباق خروجی کمپرسور با تقاضای واقعی از کارکرد غیرضروری کمپرسور جلوگیری کرده و صرفه جویی انرژی تا ۳۵% یا بیشتر را امکان پذیر می سازد.
- فناوری اینترنت اشیا (IoT) و مانیتورینگ از راه دور : کمپرسورهای اسکرو مدرن می توانند به سیستم های اینترنت اشیا (IoT) متصل شوند و داده های عملکردی را به صورت بلادرنگ (Real-time) به سیستم های مانیتورینگ مرکزی ارسال کنند. این داده ها شامل پارامترهایی مانند فشار دما جریان سطح روغن وضعیت فیلترها و هشدارهای خطا است. مانیتورینگ از راه دور امکان تشخیص زودهنگام مشکلات فنی انجام تعمیرات پیشگیرانه و بهینه سازی عملکرد کمپرسور را فراهم می کند. تحلیل داده های جمع آوری شده از طریق سیستم های IoT به شناسایی الگوهای خرابی پیش بینی زمان تعمیرات و بهبود استراتژی های نگهداری کمک می کند.
- پروفیل های روتور پیشرفته و پوشش های مقاوم در برابر سایش : توسعه پروفیل های روتور پیشرفته با طراحی هندسی بهینه تر راندمان تراکم را افزایش داده و مصرف انرژی را کاهش می دهد. استفاده از پوشش های مقاوم در برابر سایش بر روی روتورها و محفظه طول عمر واحد هواساز را افزایش داده و نیاز به تعمیرات و تعویض قطعات را کاهش می دهد. پوشش های پیشرفته مانند پوشش های DLC (Diamond-Like Carbon) و پوشش های سرامیکی مقاومت بسیار بالایی در برابر سایش خوردگی و دماهای بالا دارند.
چالش ها و محدودیت های فنی + غلبه بر موانع عملکردی
کمپرسورهای اسکرو با وجود مزایای فراوان با چالش ها و محدودیت های فنی نیز روبرو هستند که در صورت عدم توجه می توانند بر عملکرد و طول عمر آن ها تاثیر منفی بگذارند. برخی از مهم ترین چالش ها و محدودیت ها عبارتند از :
- سایش و فرسودگی روتورها و بیرینگ ها : در طول زمان سایش و فرسودگی روتورها و بیرینگ ها به دلیل تماس مداوم و بارهای سنگین اجتناب ناپذیر است. روانکاری نامناسب آلودگی روغن و شرایط کاری سخت می توانند فرآیند سایش را تسریع کنند. بازرسی های دوره ای و تعویض به موقع قطعات فرسوده از بروز خرابی های جدی تر و توقف ناگهانی کمپرسور جلوگیری می کند. آنالیز روغن به صورت دوره ای می تواند اطلاعات ارزشمندی در مورد وضعیت روتورها و بیرینگ ها ارائه دهد و زمان مناسب تعویض روغن و انجام تعمیرات را تعیین کند.
- حمل روغن (Oil Carryover) (در کمپرسورهای روغنی) : مقدار کمی روغن همواره در هوای فشرده خروجی از کمپرسورهای اسکرو روغنی وجود دارد. حمل روغن بیش از حد مجاز (Oil Carryover) می تواند منجر به آلودگی سیستم هوای فشرده کاهش راندمان سپراتور روغن و افزایش مصرف روغن شود. عملکرد نامناسب سپراتور روغن گرفتگی فیلتر روغن سطح روغن نامناسب و دمای کاری بالا می توانند از عوامل افزایش حمل روغن باشند. نگهداری صحیح سپراتور روغن تعویض منظم فیلتر روغن و کنترل دمای کاری کمپرسور به کاهش حمل روغن کمک می کند.
- تولید گرما و نیاز به خنک کاری : فرآیند تراکم هوا در کمپرسورهای اسکرو گرمای قابل توجهی تولید می کند. عدم کفایت سیستم خنک کننده می تواند منجر به افزایش دمای کاری کمپرسور کاهش راندمان آسیب به قطعات و حتی توقف کمپرسور شود. تمیز کردن منظم رادیاتورها و خنک کننده ها بررسی سطح مایع خنک کننده (در سیستم های آب خنک) و اطمینان از عملکرد صحیح فن ها از اهمیت ویژه ای برخوردار است.
- نشتی هوا (Air Leakage) : نشتی هوا در سیستم لوله کشی هوای فشرده و اتصالات کمپرسور منجر به اتلاف انرژی کاهش فشار سیستم و افزایش زمان کارکرد کمپرسور می شود. بازرسی های دوره ای و رفع نشتی های هوا به بهبود راندمان و کاهش هزینه های انرژی کمک می کند. استفاده از دستگاه های تشخیص نشتی هوا (Leak Detectors) و انجام تست های نشتی به صورت منظم روش های موثری برای شناسایی و رفع نشتی ها هستند.
- نویز و لرزش (Noise and Vibration) : کمپرسورهای اسکرو به ویژه کمپرسورهای بزرگ می توانند سطح نویز و لرزش قابل توجهی تولید کنند. نویز و لرزش بیش از حد می تواند منجر به آزار و اذیت کارکنان آسیب به تجهیزات مجاور و کاهش طول عمر کمپرسور شود. نصب کمپرسور بر روی پایه های ضد لرزش استفاده از کابین های عایق صدا و انجام سرویس و نگهداری منظم به کاهش نویز و لرزش کمک می کند. آنالیز ارتعاش به صورت دوره ای می تواند به تشخیص زودهنگام مشکلات بیرینگ ها و سایر قطعات دوار و جلوگیری از خرابی های ناگهانی کمک کند.
بیشتر بخوانید:
راز ماندگاری و بهرهوری بیشتر کمپرسور اسکرو+ چگونه عمر مفید دستگاه را افزایش دهیم؟
۵ نکته کلیدی برای نگهداری بهینه کمپرسورهای اسکرو
با رعایت ۵ نکته کلیدی زیر می توانید عملکرد بهینه کمپرسورهای اسکرو را تضمین کرده و طول عمر آن ها را به حداکثر برسانید :
- تعویض منظم روغن و فیلترها : خون حیات کمپرسور را تازه نگه دارید. روغن در کمپرسورهای اسکرو روغنی نقش حیاتی در خنک کاری روانکاری و آب بندی دارد. کیفیت و ویسکوزیته روغن با گذشت زمان و تحت تاثیر دما و آلودگی ها کاهش می یابد. تعویض منظم روغن و فیلترهای روغن هوا و سپراتور مطابق با توصیه های سازنده و برنامه زمان بندی نگهداری پیشگیرانه (Preventive Maintenance Schedule) از آسیب به قطعات داخلی کمپرسور کاهش راندمان و افزایش مصرف انرژی جلوگیری می کند. استفاده از روغن های با کیفیت و مطابق با مشخصات توصیه شده توسط سازنده از اهمیت ویژه ای برخوردار است. آنالیز روغن به صورت دوره ای می تواند اطلاعات ارزشمندی در مورد وضعیت روغن وجود آلودگی ها و سایش قطعات داخلی ارائه دهد و زمان مناسب تعویض روغن را تعیین کند. فیلترهای هوا و سپراتور نیز باید به طور منظم تعویض شوند تا از ورود آلودگی به سیستم و کاهش راندمان جلوگیری شود.
- بازرسی و نگهداری سیستم خنک کننده : دمای کمپرسور را کنترل کنید. سیستم خنک کننده نقش حیاتی در حفظ دمای کاری کمپرسور در محدوده مجاز دارد. عملکرد نامناسب سیستم خنک کننده می تواند منجر به افزایش دمای کاری کاهش راندمان آسیب به قطعات و توقف کمپرسور شود. بازرسی های دوره ای سیستم خنک کننده شامل تمیز کردن رادیاتورها و خنک کننده ها از گرد و غبار و آلودگی ها بررسی سطح مایع خنک کننده (در سیستم های آب خنک) اطمینان از عملکرد صحیح فن ها و پمپ های خنک کننده و بررسی نشتی ها است. تمیز کردن رادیاتورها می تواند به طور قابل توجهی راندمان خنک کننده را بهبود بخشد. استفاده از آب مقطر یا آب دی یونیزه شده در سیستم های آب خنک از تشکیل رسوب و خوردگی جلوگیری می کند.
- کنترل و کالیبراسیون سیستم کنترل : اطمینان از عملکرد دقیق سنسورها و کنترلرها. سیستم کنترل وظیفه مدیریت و پایش عملکرد کمپرسور را بر عهده دارد. عملکرد نامناسب سنسورها و کنترلرها می تواند منجر به عملکرد غیربهینه کمپرسور افزایش مصرف انرژی هشدارهای خطا و حتی خرابی کمپرسور شود. کنترل و کالیبراسیون دوره ای سنسورهای فشار دما و سطح روغن بررسی عملکرد صحیح کنترلرها و اطمینان از تنظیمات صحیح پارامترهای کنترلی از اهمیت ویژه ای برخوردار است. استفاده از دستگاه های کالیبراسیون دقیق و انجام کالیبراسیون توسط پرسنل آموزش دیده دقت و قابلیت اطمینان سیستم کنترل را تضمین می کند.
- بازرسی دوره ای روتورها و بیرینگ ها : علائم هشدار اولیه را شناسایی کنید. روتورها و بیرینگ ها از مهم ترین و گران قیمت ترین قطعات کمپرسور اسکرو هستند. سایش و فرسودگی این قطعات می تواند منجر به کاهش راندمان افزایش نویز و لرزش و در نهایت خرابی کامل واحد هواساز شود. بازرسی های دوره ای روتورها و بیرینگ ها شامل بازرسی چشمی از نظر علائم سایش خوردگی و آسیب آنالیز ارتعاش برای تشخیص زودهنگام مشکلات بیرینگ ها و بررسی لقی و روانکاری بیرینگ ها است. آنالیز ارتعاش به صورت منظم می تواند اطلاعات ارزشمندی در مورد وضعیت بیرینگ ها ارائه دهد و زمان مناسب تعویض آن ها را تعیین کند. در صورت مشاهده علائم هشدار اولیه مانند نویز غیرعادی لرزش بیش از حد یا افزایش دما باید اقدامات اصلاحی فوری انجام شود.
- نگهداری سیستم هوای فشرده : کیفیت هوای خروجی را تضمین کنید. کیفیت هوای فشرده تاثیر مستقیمی بر عملکرد تجهیزات پنوماتیک کیفیت محصولات و راندمان کلی سیستم هوای فشرده دارد. نگهداری سیستم هوای فشرده شامل تخلیه منظم کندانس از مخازن هوای فشرده و درایرها تعویض منظم فیلترهای هوا و سپراتورهای آب و روغن بازرسی و رفع نشتی های هوا در سیستم لوله کشی و اتصالات و بررسی عملکرد درایرها و سایر تجهیزات تصفیه هوا است. تخلیه منظم کندانس از تشکیل زنگ زدگی و خوردگی در مخازن و لوله ها جلوگیری می کند. تعویض منظم فیلترها و سپراتورها کیفیت هوای فشرده را مطابق با استانداردهای مورد نیاز تضمین می کند. رفع نشتی های هوا اتلاف انرژی را کاهش داده و راندمان سیستم را بهبود می بخشد.
نتیجه گیری+ تضمین پایداری و بهره وری با نگهداری هوشمندانه
نگهداری صحیح و منظم کمپرسورهای اسکرو نه تنها طول عمر آن ها را افزایش می دهد بلکه عملکرد بهینه راندمان بالا و کاهش هزینه های انرژی را نیز تضمین می کند. با رعایت ۵ نکته کلیدی ذکر شده و پیروی از برنامه زمان بندی نگهداری پیشگیرانه می توانید از عملکرد بی وقفه و قابل اعتماد کمپرسورهای اسکروی خود اطمینان حاصل کرده و پایداری و بهره وری فرآیندهای صنعتی خود را ارتقا دهید. سرمایه گذاری در نگهداری پیشگیرانه در بلندمدت بسیار مقرون به صرفه تر از تعمیرات اضطراری و توقف ناگهانی کمپرسورها خواهد بود. با بهره گیری از فناوری های پیشرفته مانیتورینگ و آنالیز داده ها می توان استراتژی های نگهداری را بهینه تر کرده و به سمت نگهداری مبتنی بر وضعیت (Condition-Based Maintenance) حرکت کرد. این رویکرد امکان پیش بینی زمان خرابی قطعات و انجام تعمیرات قبل از وقوع مشکل را فراهم می کند و حداکثر بهره وری و حداقل زمان توقف را تضمین می کند.
پرسش و پاسخ های متداول
هر چند وقت یکبار باید روغن کمپرسور اسکرو را تعویض کنم؟
فاصله زمانی تعویض روغن کمپرسور اسکرو بستگی به نوع روغن (مینرال سنتتیک یا نیمه سنتتیک) شرایط کاری کمپرسور (دما رطوبت آلودگی) و توصیه سازنده دارد. به طور کلی روغن های مینرال معمولاً هر ۲۰۰۰ تا ۴۰۰۰ ساعت کاری روغن های نیمه سنتتیک هر ۴۰۰۰ تا ۶۰۰۰ ساعت کاری و روغن های سنتتیک هر ۶۰۰۰ تا ۸۰۰۰ ساعت کاری یا بیشتر نیاز به تعویض دارند. آنالیز روغن به صورت دوره ای می تواند اطلاعات دقیق تری در مورد وضعیت روغن ارائه دهد و زمان مناسب تعویض روغن را تعیین کند. در شرایط کاری سخت و دماهای بالا فواصل تعویض روغن باید کوتاه تر شود.
علائم خرابی کمپرسور اسکرو چیست؟
علائم خرابی کمپرسور اسکرو می تواند متنوع باشد اما برخی از رایج ترین علائم عبارتند از : افزایش نویز و لرزش غیرعادی کاهش فشار خروجی هوا افزایش دمای کاری کمپرسور افزایش مصرف روغن (در کمپرسورهای روغنی) خروج روغن از کمپرسور هشدارهای خطا در سیستم کنترل و توقف ناگهانی کمپرسور. در صورت مشاهده هر یک از این علائم باید سریعاً نسبت به بررسی و رفع مشکل اقدام شود. نادیده گرفتن علائم اولیه خرابی می تواند منجر به آسیب های جدی تر و هزینه برتر شود.
آیا می توانم نگهداری کمپرسور اسکرو را خودم انجام دهم یا نیاز به متخصص دارم؟
برخی از اقدامات نگهداری روتین مانند تعویض روغن و فیلترها تمیز کردن رادیاتورها و تخلیه کندانس را می توان با آموزش مناسب و رعایت دستورالعمل های سازنده توسط پرسنل داخلی انجام داد. اما تعمیرات تخصصی تر مانند تعمیر یا تعویض واحد هواساز سیستم کنترل و سیستم روغن کاری نیاز به دانش فنی تخصصی ابزارآلات خاص و تجربه دارد و باید توسط تکنسین های مجرب و متخصص انجام شود. همکاری با یک شرکت خدمات نگهداری معتبر و متخصص می تواند اطمینان از انجام نگهداری صحیح و به موقع کمپرسور و جلوگیری از مشکلات جدی تر را فراهم کند.